Smart Tool Tracking for Job Sites With AI-Powered RFID Technology
- Smart Toolcase
- Feb 12
- 5 min read
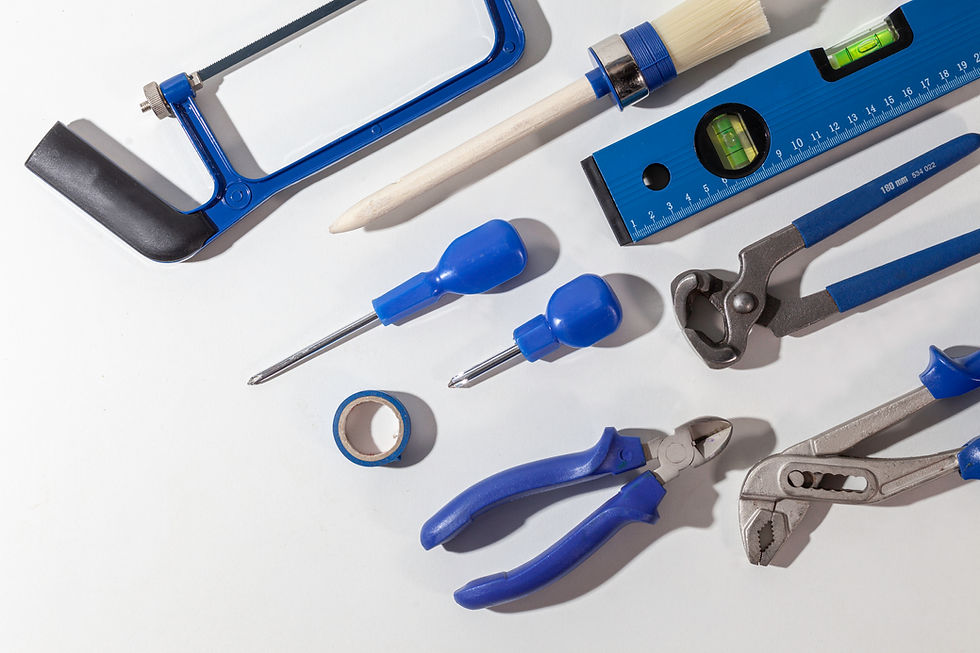
Losing tools on the job site leads to wasted time, increased costs, and project delays. Construction companies and independent contractors struggle with misplaced or stolen equipment, often realizing too late that key tools are missing. Traditional tracking methods, such as manual checklists, barcode scanning, or simple toolboxes, rely on human effort, making them inefficient and prone to errors.
Toolcase offers a smart, automated solution that helps workers keep track of their tools using RFID technology and AI-powered tracking. Unlike outdated systems, Toolcase scans, tracks, and alerts users in real-time, making it easier to manage tools before leaving a job site. With automatic scanning, dynamic triangulation, and smartphone integration, Toolcase improves productivity, reduces financial losses, and simplifies inventory management.
The Cost of Losing Tools on the Job Site
Misplaced or stolen tools cost companies thousands of dollars every year—not only in direct replacement costs but also in lost productivity and project delays. Many workers spend valuable time searching for missing equipment, and in some cases, companies repurchase tools left behind at a previous site. These unnecessary expenses add up, impacting overall profitability.
One major challenge is manual tracking. Many job sites still rely on written logs, spreadsheets, or barcode scanners to track tools. These outdated methods require constant supervision and depend on workers remembering to log every tool they use. In a fast-paced work environment, mistakes happen—a tool may be borrowed without being checked out, or an employee may forget to scan an item before moving it to another location. Without real-time visibility, tools can become missing without a clear way to recover them.
Tool theft is another serious issue. Construction sites are prime targets, especially for expensive equipment. Many job sites lack security during off-hours, making tools easy targets. A missing drill or saw might seem like a small loss, but multiple stolen tools over time can result in significant financial setbacks. Additionally, some tools disappear not due to theft but simply because they are left at a previous site, buried under materials, or misplaced in another vehicle.
A final issue is traditional tracking systems' inefficiency. Barcode-based inventory requires direct scanning of each tool, which takes time and effort. RFID-based tracking exists, but many systems still require manual scanning or cannot track the real-time tool movement. Companies struggle to maintain full control over their inventory without an automated tracking and alert system.
This is where Toolcase provides a better approach. By offering an AI-powered, RFID-based tool management system, it prevents human error and keeps all tools accounted for. The system automatically tracks all registered tools, alerts users when something is missing, and provides precise location data, saving time, money, and effort.
How Toolcase Improves Tool Tracking
Traditional tool tracking methods require workers to manually log or scan each tool, leaving room for errors and inefficiencies. Toolcase simplifies this process with an intelligent RFID-based tracking system that continuously monitors tools without additional effort from workers.
The system operates using RFID tags that attach to individual tools. These tags communicate with a compact RFID reader placed inside a toolbox or work vehicle. As tools enter or exit the designated storage area, the reader detects their movement and updates the inventory in real-time. This removes the need for manual tracking and helps workers instantly see which tools are present and which are missing.
Toolcase's key feature is its dynamic triangulation technology. Unlike basic RFID scanners that only confirm if a tool is within range, Toolcase calculates the precise location of each tagged tool. By constantly pinging RFID tags and analyzing their relative positions, the system provides real-time tracking down to an accuracy of 5mm. This level of precision allows workers to quickly retrieve misplaced tools without unnecessary searching.
The smartphone application further enhances usability by integrating inventory management features. Workers can use the app to assign tools, update records, and receive alerts when a tool is missing. If a tool is left behind at a job site, Toolcase immediately notifies the user before they leave. This prevents expensive mistakes and reduces the time spent retrieving forgotten equipment.
Toolcase also adapts to different work environments by supporting both active and passive RFID tags. Active RFID tags have an extended range, making them suitable for tracking tools across large job sites, while passive RFID tags offer a cost-effective option for smaller workspaces. Regardless of the tag type, the system assures that all tools remain accounted for without physical scanning.
Another major advantage is Toolcase’s ability to detect movement patterns. The system can identify if a tool is being taken out of the designated area without authorization, making it an effective deterrent against theft. If a tool is moved beyond a set distance, the app sends an alert to the owner, allowing them to act before the tool is lost.
AI and Smart Inventory Management
Beyond RFID tracking, Toolcase incorporates AI technology to optimize tool inventory management. Traditional tracking systems only detect whether tools are present or missing, but Toolcase takes it further by analyzing usage patterns and predicting potential issues.
One of the key AI-driven features is smart tool recognition. Workers can take a picture of their tools through the Toolcase app, and AI automatically labels them. This reduces the need for manual data entry and speeds up RFID tag assignment. Over time, the system learns from usage patterns and improves its ability to identify tools accurately.
Toolcase also help with predictive maintenance. By tracking how often tools are used and for how long, the system can notify workers when they are due for maintenance or replacement. This prevents unexpected breakdowns and guarantees that the equipment remains working.
AI also optimizes tool allocation. By analyzing tool usage data, the system identifies which tools are frequently used and which ones are rarely needed. This allows companies to make informed decisions about purchasing new tools or redistributing existing equipment to different job sites.
Another benefit is automated inventory audits. Instead of requiring workers to manually check tools at the end of the day, Toolcase can run scheduled scans and generate reports on missing or misplaced tools. This reduces workers' administrative burden and guarantees that the tools are always where they need to be.
Security is another important aspect of AI-driven inventory management. Toolcase’s intelligent monitoring system can detect unusual tool usage patterns, such as tools being moved outside normal working hours. If suspicious activity is detected, the system immediately sends an alert, preventing theft and unauthorized tool use.
Smart Tool Management for a More Efficient Job Site
Keeping track of tools is a constant challenge on job sites, but with advancements in technology, managing equipment has never been easier. Toolcase provides a practical, intelligent solution that simplifies inventory management while reducing tool loss and theft.
By integrating RFID tracking with AI-driven insights, Toolcase automates monitoring tools, making it easier to always know where equipment is located. Real-time alerts and precise tracking features prevent misplaced or stolen tools, saving businesses time and money. Additionally, predictive maintenance and automated inventory audits improve tool management, allowing workers to focus on their tasks instead of manually checking equipment.
With its combination of real-time tracking, AI-enhanced inventory management, and easy-to-use mobile integration, Toolcase changes the way professionals handle their tools. For any job site looking to improve efficiency, security, and organization, investing in a smart tool-tracking system is a step in the right direction.
コメント